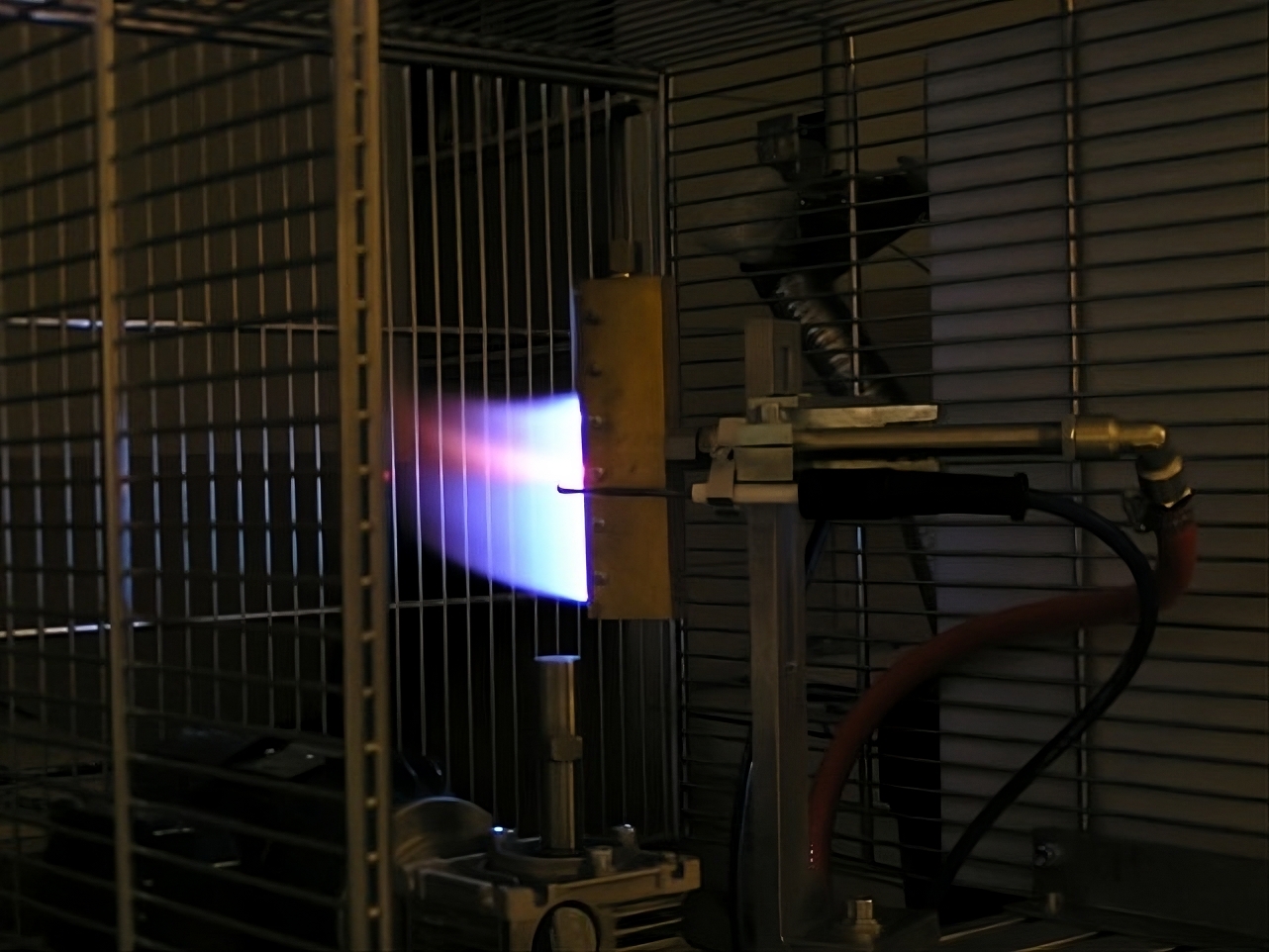
FireDrake is a brand of Polish surface activation devices designed for plastic and glass applications, which Tampotechnika Sp. z o.o. has been producing for 30 years.
One of the most frequent issues occurring in the manufacturing of plastic products is insufficient adhesion between the ink, lacquer or glue, and the surface material. The fluid doesn’t wet the surface, instead it turns into droplets. This negatively impacts the quality of the end product. The solution to this problem is surface activation, a process which increases the surface energy of the product to a level sufficient to break the surface tension of the fluid which is being used.
To confirm if surface activation is needed, it is necessary to measure the surface energy of the surface material. We offer tester pens for determining the surface energy of various materials and surface cleanliness levels. If a line drawn by a tester loses its shape, it means that the surface energy is lower than the surface tension of the fluid being tested, and surface activation is needed.
The simplest type of surface activation is chemical activation. We offer the PP Primer fluid, which is applied on the surface with a cloth. After drying it creates an activated surface with sufficient adhesion for many types of ink and glue. The primer fluid is most often used in small to medium manufacturing.
Another way of increasing surface energy is treating the product surface with plasma. The plasma creates radicals on the product surface, molecules which contain an unpaired electron, and this increases the wettability of the surface.
Flame treatment is the most frequently used method of activation due to its high effectiveness, low cost and large activation surface. It works by burning flammable gas (propane-butane, natural gas) mixed with excessive oxygen. The shape of the flame and its reaction zone, as well as fuel consumption, depend on the type of burner used. The burners are automatically controlled (combustion and flame detection) and have covers which keep them from causing a fire or burning the operator. We offer handheld, semiautomatic and fully automatic FireDrake flame treatment solutions, ranging from handheld burners to setups, where a burner is moved in a programmed trajectory by an industrial robot.
A particular method of flame treatment is the PYROSIL® process, in which a silicate suspension (a precursor) is added to the flame, which leads to greatly increased activation efficacy. We offer solutions for PYROSIL® activation of plastics, glass and metals, which are to be lacquered, printed on or glued.
Corona treatment and modification of surface properties using atmospheric plasma is the cutting edge in activation technology. We offer solutions manufactured by Tantec A/S, a specialist in this field. They are characterized by their high efficiency and safety and ease of use. They can successfully be used in production lines. The addition of gaseous or liquid admixtures (precursors) allows the surface to gain special properties. Besides achieving optimum wettability, the surface can become impermeable, hydrophobic or dielectric. Atmospheric plasma can also be used to clean the products without the use of thinners.